Summer is a busy time in the construction business. While projects can be done year-round, the warm summer months are peak time to complete outdoor projects with longer hours of daylight and less chance for freezing temperature or snow. (We do live in the Midwest, so you never know, right?)
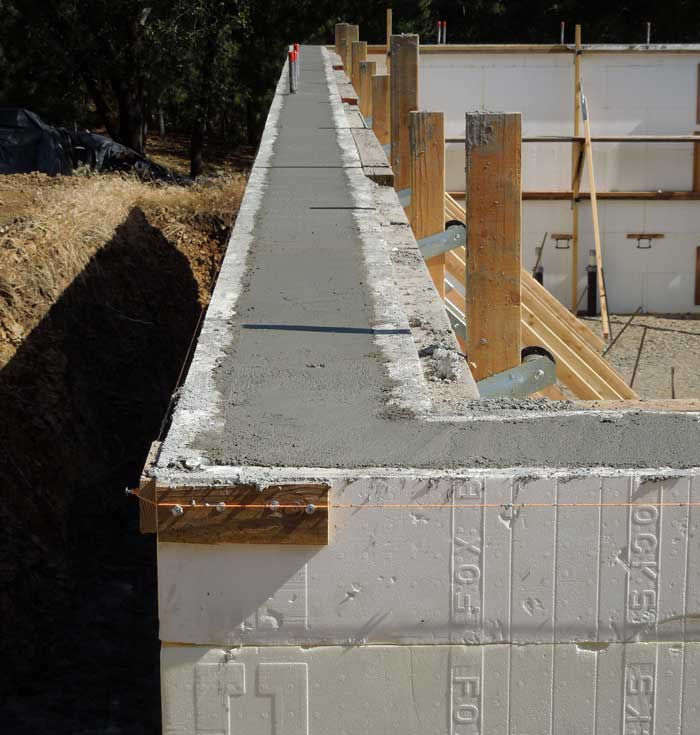
Building season is especially busy now as construction companies continue to play catch-up after the shut-down during the COVID-19 pandemic. Many companies had to halt work for weeks - even months. During that time, more projects came in as people who were now stuck at home decided it was time to start some renovations or build a new home.
Many contractors have projects their company can not start working on for three to six months out minimum and face another issue when it finally comes time to complete the job. Cost.
Material costs have gone up significantly in the past year and builders have no choice but to pass the cost onto their customers. One area in particular has taken a surprising leap. Lumber prices have risen sharply in the last six months. According to the National Association of Home Builders, lumber prices have tripled in the past year (April 2020 - April 2021). As of the week of April 23, 2021, “the price of framing lumber sits at $1,200 per thousand board feet - up nearly 250 percent since April when the price was roughly $350 per thousand board feet,” according to a report by the NAHB.
But what has this got to do with concrete? Well, a lot, actually.
Think concrete
Houses still need to be built and homeowners are looking for the most cost effective solutions. With the cost of lumber at an all-time high, it’s time to think concrete.
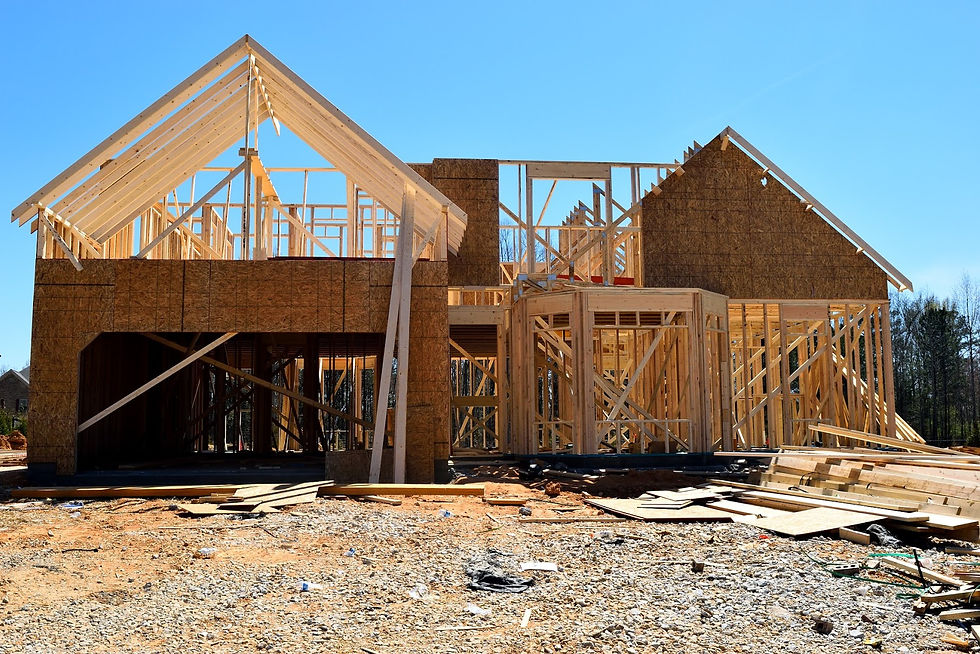
While lumber is used in many facets of the home, concrete is a cost-effective alternative. Lumber prices may be soaring, but concrete has leveled out (please excuse the bad concrete pun) in terms of cost and in most communities in either the same price or lower that lumber. It can also oftentimes be more readily available than lumber is currently.
Easy to install

Insulated Concrete Forms (ICFs) are large pre-made forms that fit together like interlocking blocks. The forms are made from high-density foam and are filled with concrete. The forms are easy to put together, stay in place and are reinforced with steel. The use of insulated concrete forms also consolidates several building steps into one. Contractors can build walls in as little time as a day as the forms are sturdy and still in place. This cuts down not only on labor costs for installation, but for the overall time to construct the home.
ICFs can be used both in foundations and above grade walls of a structure. Concrete built homes look exactly like stick built homes as ICFs come with nailing strips allowing for interior finishes like drywall and exterior finishes like siding and stucco.
The ease of installation is just one of the advantages of ICFs. Along with time saved in building our home, homeowners will also save money with an ICF build house. Concrete forms are solid structures that are super insulated keeping your house warm and cozy in the winter and cool and comfortable in the summer. ICFs are ideal for Midwest climates which fluctuate often.
The benefits of ICF continue once your house is built! ICF homes are less drafty than wood homes and have fewer cold spots, maintaining a more even temperature throughout the home.
Stronger, safer structure
Movement is greatly reduced in an ICF-built home. Concrete walls are stronger than wood built walls in many ways and homeowners will not feel flex in walls or floors and virtually no vibration when slamming doors. With less movement through the home, there is less noise as well. ICF homes have noticeably less noise reducing sound both inside and outside the structure by as much as 80 percent compared to a wood built home.
Homes built using ICFs can prove to be safer as well. In the event of a tornado, “ICF walls protected the owners and their pets from the fierce wind and debris even when the roof was gone,” states a report from the U.S. Department of Housing and Urban Development. Concrete forms also hold up well during hurricanes and floods.
In the event of a fire, an ICF built home can be life saving. Insulated concrete forms are treated with flame retardants to prevent them from burning. According to an article from the Concrete Network, “In fire-wall tests, ICF and concrete walls withstood continuous exposure to intense flames and temperatures of up to 2,000 degrees F for as long as 4 hours without structural failure, compared with wood-frame walls that collapsed in an hour or less.”
Greener homes
Homes built with ICF will provide homeowners significant reductions in energy consumption and emissions while providing a stronger, quieter and more comfortable home. For those looking to build a “greener” home the higher quality insulation of ICFs and smaller HVAC units equals lower fossil fuel consumption. A concrete house will therefore generate fewer greenhouse emissions over the life of the home than a wood built home.
Building with energy efficient materials for houses like insulated concrete forms may also qualify buyers for an Energy Efficient Mortgage (EEM). This type of mortgage can give the homeowner special benefits when purchasing a home that is energy efficient or can be made efficient.
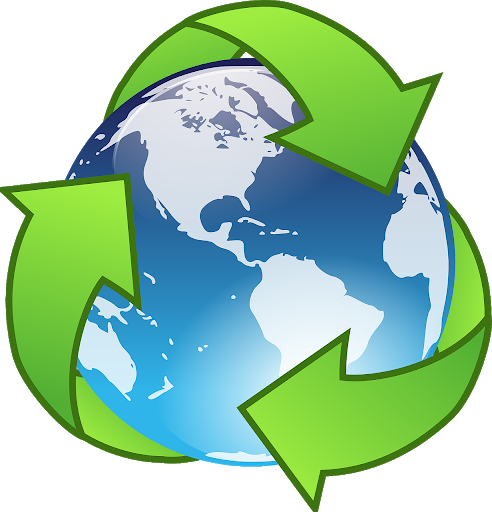
An ICF built home will be less popular - with pests that is. A home with walls of concrete is less desirable than a wood build home that pests like termites, ants and other rodents like to eat or build a home in. Since concrete is made with no no organic materials, mold and mildew will not grow. Concrete also minimizes the league of radon gas into the home as well as other harmful allergens. Concrete will maintain for years to come. Untreated lumber will rot and deteriorate, but concrete will not crumble, Concrete Stands the Test of Time! The steel used inside the ICFs will also not rust.
Boost Bottom Line
Finally a home built using ICFs will add more money to your pocket not only when it comes to saving energy, but it’s time to sell. Building with insulated concrete forms can boost your property value by creating a green MLS listing (which will make your home stand out),adding value to appraisals, and bringing in higher resale values.

Becker and Scrivens recommends the Fox Blocks ICF system when considering insulated concrete forms for your structure.
Becker & Scrivens of Hillsdale and Montpelier Ohio is the leading redi mix concrete supplier in the area. Tell your contractor you want Becker & Scrivens concrete for your next construction project.
Comments